Across industries from life sciences to electronics, ultra-high resolution and precision parts are often required for innovation – especially when that innovation is driven by miniaturization. As products and technology get smaller, so do the intricacies of the parts that are the sum of the whole. Many engineers and product designers are turning to 3D printing to manufacture these highly precise, small-scale parts. Additive manufacturing is lately proving to be an efficient option when compared to traditional molding.
Micro-3D printing is used to create high-precision tiny parts for medical devices, optics, photonics, microfluidics, and consumer packaged goods. Many of these parts have become the backbone of personalized healthcare devices. They are also utilized widely in aerospace and automotive.
To get a deeper look into developments in micro-3D printing, we checked in with John Kawola, CEO of Global Operations at Boston Micro Fabrication (BMF).
What are the advantages of micro-scale 3D printing in producing parts?
John Kawola: For many years, creating molds for prototyping was the only solution for micro parts, but that method was time-consuming and costly. Today, many industries and applications use additive manufacturing as a cost-effective option for on-demand prototyping and production, but it also allows engineers to push the boundaries of innovation.
At BMF, our customers are often looking for a level of precision that is simply impossible to achieve with traditional manufacturing methods like machining or molding. BMF’s Projection Micro Stereolithography (PµSL) technology allows customers to consistently achieve extremely small features with high-precision, resolution, and accuracy.

Image courtesy of Boston Micro Fabrication.
We’ve also started to develop end-applications where we feel our technology is uniquely suited for addressing industry pain points. For example, UltraThineer veneers – the world’s thinnest cosmetic dental veneers – would not be possible to create without micro-scale 3D printing.
Explain the need for larger parts with the precision and quality associated with micro-scale manufacturing.
John Kawola: High precision isn’t just important for micro-sized parts. As product design continues to be a driver of innovation, the demand for highly precise and accurate parts remains, regardless of part size. While BMF is often associated with micro prints, which are at the core of our business, we can also print larger parts with a build area of 100 x 100 x 75mm. We built our microArch S350 platform specifically to address a market need for people who need high accuracy and precision, but not at the very high resolution of our other systems. It’s a 25µm platform that can print at faster speeds using engineering-grade materials to enable manufacturers who may not need super high resolution, but to whom accuracy and precision are important.
How has BMF redefined the conventional limits of size in additive manufacturing? And why was this necessary?
John Kawola: Prior to BMF, there were no options available to prototype micro sized parts with complex geometries and small features outside of traditional manufacturing methods, such as micro injection molding. What many companies find is that the smaller the part, the more challenging and costly it is to manufacture using traditional methods. Our PμSL technology leverages light, customizable optics, a high-quality movement platform and controlled processing technology to produce the industry’s most accurate and precise high-resolution 3D prints for product development, research and industrial short run production.
At BMF, we provide advanced manufacturing solutions for ultra-high precision applications because we saw a market need for micro-precision parts with dimensional accuracy and precision across industries and in the different stages of product development from prototyping to production.
What was required to develop automation and speeds needed for short-run production of ultra-high-resolution parts?
John Kawola: The ability to get high resolution, accuracy and precision with 3D printing is dependent on multiple factors. These include the resolution of the optics, the precision of the mechanical systems in the machine, the control of the exposure and the resultant curing, the interaction between the part and required support structures, and, lastly, the overall size of the part and the ability to control tolerances across the build.
Each of our printers has features that contribute to a step-and-repeat process that allows for parts with high resolution and controlled processing technology to produce highly precise objects. The entire microArch collection also includes a customizable high-resolution optical system and movement platform, real-time image monitoring, auto focus and exposure compensation, and operation software with a streamlined interface and customer parameter settings. The microArch 3D printing system is able to realize ultra-high resolution, large-area printing that is used in industrial prototyping and short-run production.
Explain the refinements in hardware, software, and material science needed to accomplish this.
John Kawola: BMF’s 3D printers use PµSL technology, which is a form of stereolithography (SLA) that incorporates a DLP® light engine, precision optics, motion control, and advanced software. SLA produces parts in layers using a photochemical process. A photosensitive liquid resin is exposed to light so that polymeric cross-linking and solidification occurs. With PµSL technology, a flash of ultraviolet (UV) light causes the rapid photopolymerization of an entire layer of resin.

Image courtesy of Boston Micro Fabrication.
The PµSL process we use is top down. The top-down scheme not only minimizes the number of support structures required, but also provides a way to reduce the damage to small features and remove bubbles using a scraper that runs across a transparent membrane. No supports are needed to secure the bottom surface to the print surface and limited supports are required for overhangs due to the interaction of often light weight parts and buoyancy of the resin. PµSL systems from BMF can achieve XY resolution down to 2 µm, minimum feature size of 10 µm and dimensional tolerance as tight as +/- 10 µm, the technology supports continuous exposure for faster processing.
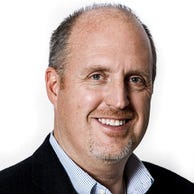
Image courtesy of Boston Micro Fabrication.
John Kawola is CEO for Global Operations of Boston Micro Fabrication (BMF). He has more than two decades of business leadership experience across the additive manufacturing, 3D printing and materials science industries. BMF is focused on introducing and scaling micro-3D printing technology to a range of industries that demand a high level of resolution and precision.